
847.673.4292
ASK US!
High Volume Multi-Spindle Screw Machining
Precision Multi Spindle Screw Machining -
the work horse
70,000 sq ft of Multi-Spindle Screw Machines for efficiency and lower costs
Need high-volume, precision machined parts? R.F. Mau Company delivers. Our facility is optimized for rapid, mid- to high-volume manufacturing of BRASS aluminum, and copper components..
For over 90 years, our family-owned and operated business has been a trusted partner for precision machined parts. Our core competency is high-volume screw machining, utilizing a substantial fleet of 50+ multi-spindle machines (New Britain, Tornos, Euroturn) to handle runs from 10,000 to millions of pieces, with diameters ranging from 1/4" to 2 1/4". These machines are the workhorses of our operation, with each spindle acting as an independent lathe, allowing for simultaneous operations (forming, drilling, threading, tapping, slotting) and rapid part production.
Automated bar feeding and conveyor systems enable continuous production, while our multi-operation capabilities from a single setup maximize speed and efficiency.
We adhere to industry standards (Mil-Spec, NSF, ANSI, ASME) and operate an advanced quality management program. Get your parts faster with R.F. Mau. Contact us today.
Watch this QUICK video


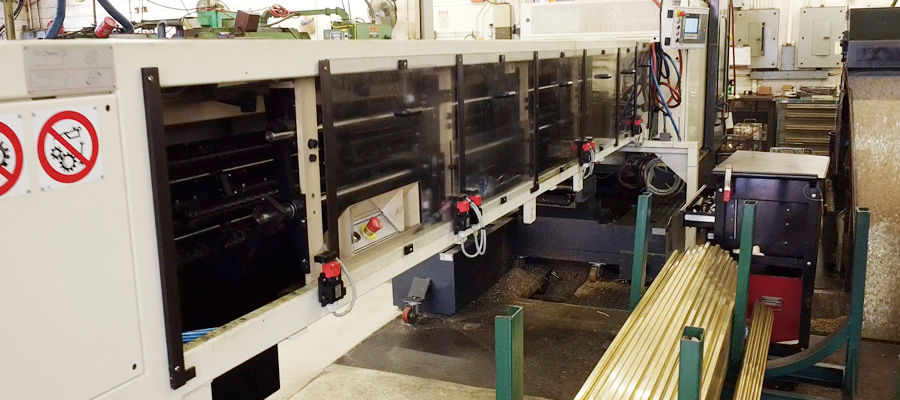
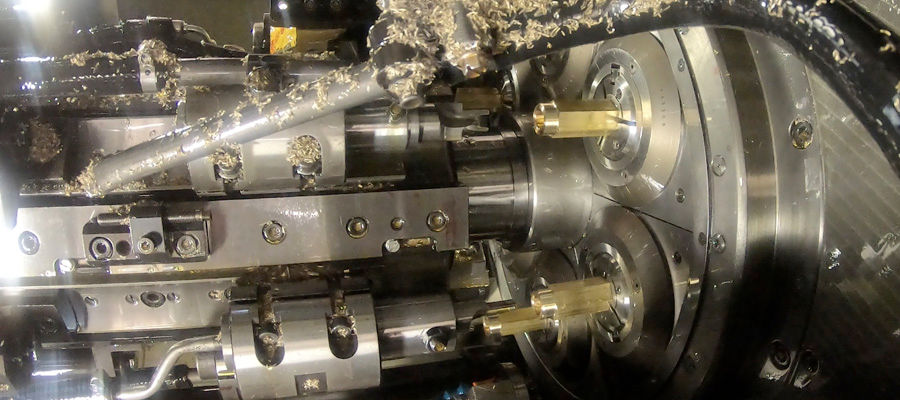


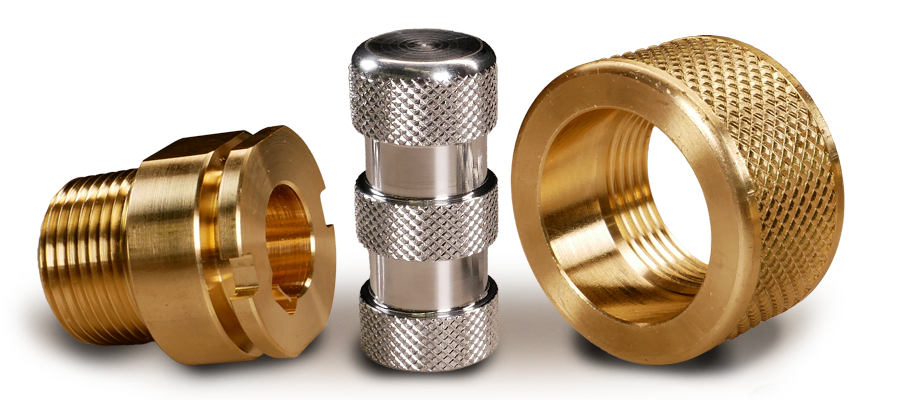
Screw Machining Advantages
-
Fast Cycle Times - Screw machines are designed for rapid, automated production. Multiple parts can be machined simultaneously, significantly reducing cycle times.
-
Continuous Operation - These machines can run often with automated bar feeders, minimizing downtime and maximizing output. This makes them ideal for large production runs.
-
Reduced Labor Costs - Due to the automation and high output, screw machining can significantly reduce labor costs per part, making it a cost-effective solution for large orders.
-
Tight Tolerances - Screw machines are capable of holding very tight tolerances, often within ±.0005" or even finer. This makes them ideal for parts requiring high precision and accuracy.
-
Consistent Quality - The automated nature of screw machining ensures consistent part quality throughout the production run, minimizing variations and defects.
-
Complex Geometries - Screw machines can produce parts with complex shapes and intricate details, often in a single setup, reducing the need for secondary operations.
-
Lower Per-Part Cost: The high production speeds and automated operation lead to lower per-part costs, especially for large volumes.
-
Variety of Sizes: While often used for small parts, screw machines can handle a range of sizes, although they are generally best suited for parts under a few inches in diameter.
-
Multiple Operations: Screw machines can perform multiple machining operations simultaneously (turning, drilling, milling, threading, etc.), reducing the need for secondary operations and saving time.
In summary, screw machining is the ideal choice when:
-
High-volume production is required.
-
Tight tolerances and precision are essential.
-
Cost-effectiveness is a primary concern.
-
Complex part geometries are involved.
-
Consistent quality is critical.

High-Volume Screw Machining EQUIPMENT LIST:
Our primary machining capabilities are built around a substantial fleet of multi-spindle automatic screw machines, ensuring efficient, high-volume production:
-
New Britain:
-
10 - Model 52 (1 1/4" capacity, 6-spindle)
-
4 - S&M Model 664 (1 1/2" capacity, 6-spindle)
-
6 - Model 62 (2 1/4" capacity, 6-spindle)
-
3 - Model 81 (1" capacity, 8-spindle)
-
2 - Model 814 (1 1/4" capacity, 8-spindle)
-
4 - (1 1/2" capacity, 6-spindle)
-
-
Euroturn:
-
4 - Model 632 (1 1/4" capacity, 6-spindle)
-
2 - Model 832 (1 1/4" capacity, 8-spindle)
-
2 - Model 842 (1 5/8" capacity, 8-spindle)
-
-
Tornos:
-
5 - SAS 16.6 (.656" capacity, 6-spindle)
-
Secondary Operations & CNC Machining:
To provide complete, finished parts, we also offer a range of secondary operations and CNC machining capabilities:
-
9 - MSO Rotary Transfer Machines
-
1 - Daewoo Puma 240 MS CNC Turning Center (up to 2.500" diameter)
-
4 - Haas CNC Mini Mills
-
4 - Haas CNC Lathes
-
Supplementary milling, drilling, tapping, and broaching machines
